I had really good success with making the side curtain frames, and was happy with the result.............but...........
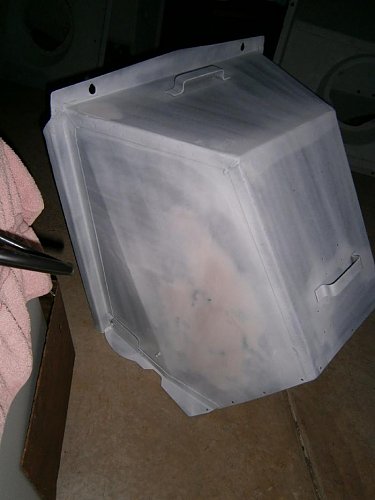
got no joy with the work on engine cover, in fact the phrase 'total bollocks up' comes to mind! A patch was shaped, welding started, and then the problems started. First, heat pulled the metal more than I had expected. I alternated weld sites and allowed each to cool sufficiently before continuing, but it still shrunk the metal like I had never seen before. In photo 2, you can just see the filler under the 'emergency' coat of etch. I only got as far as etch before I ran out of day.
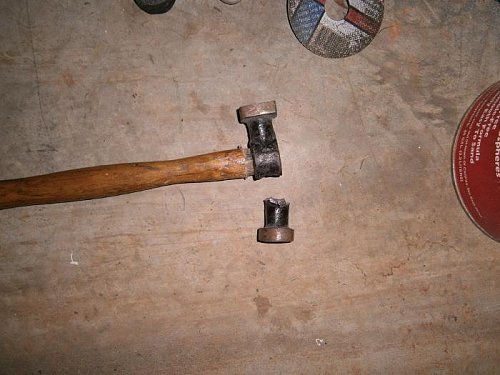
I guess the work required to stretch the metal back to some semblence of normal was just too much for the poor old hammer!

I found this acoustic/heat shield at the local rubber shop. It's adhesive backed and supposed to be easy to apply. I had intended to cut it to desired sizes today. That didn't happen because of the time I spent whacking the engine cover into shape. Not the right shape you understand, close, but definately not right. I am not pleased with losing definition of one of the metal creases on welded side. As Dirty Harry once said...." A Man's Got to Know His Limitations". God I HATE panelbeating